Berbagai faktor yang mempengaruhi stabilitas dimensi coran investasi
Terus meningkatkan akurasi dimensi coran investasi dan mengurangi produk limbah yang disebabkan oleh oversize selalu menjadi salah satu tujuan utama yang dikejar oleh pekerja pengecoran investasi di dalam dan luar negeri.
1. Stabilitas dimensi coran investasi
1. Stabilitas dimensi model lilin dan faktor-faktor yang mempengaruhinya
Dalam kebanyakan kasus, ukuran cetakan lilin sangat berfluktuasi ketika ukuran cetakan berfluktuasi, dan ada beberapa pengecualian. Secara keseluruhan, fluktuasi ukuran cetakan lilin menyumbang 10% hingga 70% dari fluktuasi ukuran casting.
Parameter proses pencetakan memiliki pengaruh yang menentukan pada stabilitas dimensi cetakan lilin. Faktor utamanya adalah sebagai berikut:
(1) Suhu pengepresan lilin
Bahan cetakan yang berbeda memiliki kinerja yang berbeda karena pengaruh suhu pengepresan lilin. Ketika bahan cetakan berbasis lilin digunakan, suhu pengepresan lilin sangat sensitif terhadap pengaruh stabilitas dimensi cetakan lilin, sedangkan bahan cetakan berbasis resin memiliki pengaruh yang lebih kecil.
(2) Tekanan injeksi
Ketika tekanannya kecil, tingkat penyusutan cetakan lilin berkurang secara signifikan ketika tekanan meningkat. Namun, setelah tekanan dinaikkan sampai batas tertentu (≥1.6MPa), tekanan hampir tidak berpengaruh pada ukuran cetakan lilin. Tidak heran jika hasil tes asing sering menyimpulkan bahwa "tekanan tidak ada hubungannya dengan ukuran cetakan lilin", tetapi kesan banyak perusahaan domestik tidak sepenuhnya sama.
(3) Laju aliran
Laju aliran bahan cetakan dapat diubah dengan dua cara berikut, tetapi pengaruhnya terhadap ukuran cetakan lilin tidak sama:
·Dengan mengubah pengaturan kecepatan aliran mesin press lilin, metode ini memiliki sedikit efek pada penyusutan cetakan lilin. Namun, ini memiliki pengaruh penting pada pengisian dan kualitas permukaan bagian berdinding tipis dengan bentuk kompleks atau cetakan lilin dengan inti.
·Metode ini memiliki pengaruh besar dengan mengubah luas penampang port injeksi lilin, karena meningkatkan luas penampang port injeksi lilin tidak hanya dapat mengurangi suhu pengepresan lilin, tetapi juga memperpanjang pemadatan waktu bahan cetakan di port injeksi lilin, sehingga meningkatkan pemadatan cetakan lilin. Tingkat penyusutan dan penyusutan permukaan berkurang.
(4) Waktu injeksi
Yang disebut waktu injeksi di sini mencakup tiga periode waktu pengisian, pemadatan, dan pemeliharaan. Waktu pengisian mengacu pada waktu bahan cetakan untuk mengisi rongga cetakan; pemadatan mengacu pada waktu dari pengisian cetakan hingga penutupan nosel injeksi lilin; dan holding mengacu pada waktu dari penutupan nozzle injeksi lilin hingga pengusiran cetakan.
Waktu injeksi memiliki pengaruh yang signifikan terhadap tingkat penyusutan cetakan lilin. Hal ini karena lebih banyak bahan cetakan dapat diperas ke dalam rongga dengan meningkatkan waktu injeksi, dan cetakan lilin akan lebih padat, sehingga mengurangi tingkat penyusutan. Berat model lilin meningkat dengan waktu pemadatan yang berkepanjangan. Waktu pemadatan harus tepat. Jika waktu pemadatan terlalu lama, bahan cetakan di port injeksi lilin telah sepenuhnya dipadatkan, dan pemadatan tidak akan berfungsi. Juga dapat dilihat dari Gambar 4 bahwa ketika waktu injeksi pendek (15-25 detik), suhu pengepresan lilin meningkat, dan laju penyusutan meningkat; tetapi ketika waktu injeksi diperpanjang hingga 25-35 detik (di bawah premis bahwa waktu pengisian tetap konstan, yang sebenarnya di atas adalah untuk memperpanjang waktu pemadatan) Pengaruh suhu pengepresan lilin menjadi lebih kecil; ketika waktu injeksi meningkat menjadi lebih dari 35 detik, situasi sebaliknya akan terjadi, yaitu, ketika suhu pengepresan lilin naik, laju penyusutan cetakan lilin akan menurun. Fenomena ini dapat dijelaskan bahwa peningkatan suhu bahan cetakan dan perpanjangan waktu pemadatan memiliki efek yang sama dengan peningkatan derajat pemadatan cetakan lilin.
(5) Suhu cetakan dan peralatan pengepresan lilin
Suhu cetakan tinggi, cetakan lilin mendingin perlahan, dan tingkat penyusutan meningkat. Hal ini karena cetakan lilin masih dalam cetakan kompresi sebelum cetakan dikeluarkan, dan penyusutan terbatas, tetapi setelah cetakan dikeluarkan, menjadi bebas untuk menyusut. Oleh karena itu, jika suhu cetakan lilin tinggi saat cetakan dilepaskan, tingkat penyusutan akhir akan besar, dan sebaliknya, tingkat penyusutan akan kecil.
Dengan cara yang sama, sistem pendingin dari mesin press lilin mungkin memiliki dampak sekitar 0.3% pada ukuran cetakan lilin.
Akhirnya, perlu ditekankan bahwa ketika menggunakan bahan cetakan berbasis lilin, pasta lilin adalah sistem koeksistensi tiga fase padat, cair dan gas. Rasio volume antara tiga fase memiliki pengaruh besar pada ukuran cetakan lilin. Hubungan proporsional antara ketiganya tidak dapat dikontrol dalam produksi aktual, yang juga merupakan alasan penting untuk stabilitas dimensi yang buruk dari cetakan lilin menggunakan bahan cetakan berbasis lilin.
2. Pengaruh bahan cangkang dan proses pembuatan cangkang pada stabilitas dimensi coran
Pengaruh cangkang cetakan pada ukuran casting terutama disebabkan oleh ekspansi termal dan deformasi termal (temperatur tinggi) dari cangkang cetakan selama pembakaran, dan pembatasan (penghalang) cangkang cetakan pada penyusutan pendinginan dari cetakan. pengecoran.
(1) Ekspansi termal shell
Terutama tergantung pada bahan cangkang. Bahan tahan api yang berbeda memiliki tingkat ekspansi yang berbeda. Di antara refraktori yang umum digunakan, silika leburan memiliki laju ekspansi terkecil, diikuti oleh aluminium silikat, dan silika adalah yang terbesar dan tidak rata. Setelah pengujian, ditentukan bahwa cangkang aluminium silikat dapat dipanaskan dari suhu kamar hingga 1000 , cangkang dapat menghasilkan sekitar 0.25% ekspansi, yang menyumbang sebagian kecil dari keseluruhan penyusutan ukuran pengecoran. Oleh karena itu, jika bahan tahan api seperti itu digunakan, cangkangnya memiliki stabilitas dimensi yang lebih baik, seperti silika yang menyatu pasti akan lebih baik. Namun, jika silika digunakan, ukuran cangkang sangat berfluktuasi.
(2) Deformasi termal (creep suhu tinggi)
Misalnya, cangkang yang menggunakan gelas air sebagai pengikat memiliki tingkat creep yang jauh lebih besar pada suhu tinggi di atas 1000 °C daripada cangkang sol silika dan etil silikat. Meskipun korundum yang menyatu itu sendiri memiliki refraktori yang tinggi, karena adanya pengotor seperti natrium oksida, suhu pembakaran cangkang yang lebih tinggi dari 1000 juga dapat menyebabkan creep, yang mengakibatkan stabilitas dimensi yang buruk.
(3) Pengekangan cangkang cetakan pada penyusutan casting—penurunan dan keruntuhan cangkang cetakan Ini juga terutama tergantung pada bahan cangkang cetakan.
Singkatnya, bahan tahan api memainkan peran utama dalam pengaruh cangkang pada fluktuasi ukuran casting, tetapi peran pengikat tidak dapat diabaikan. Sebaliknya, dampak dari proses pembuatan cangkang kecil.
3. Pengaruh tegangan yang disebabkan oleh pendinginan coran yang tidak merata pada stabilitas dimensi
Laju pendinginan setiap bagian dari pengecoran (termasuk sistem gating) berbeda, yang menghasilkan tegangan termal dan merusak bentuk coran, sehingga mempengaruhi stabilitas dimensi. Hal ini sering ditemui dalam produksi yang sebenarnya. Mengurangi laju pendinginan coran dan meningkatkan kombinasi runner adalah tindakan pencegahan yang efektif.
2. Kunci untuk meningkatkan tingkat penyusutan cetakan yang akurat ditetapkan dengan benar
"Stabilitas dimensi" yang disebutkan di atas berbeda dari "akurasi dimensi" dan "presisi (presisi)". Stabilitas dimensi (yaitu presisi) identik dengan konsistensi dimensi, yang mencerminkan tingkat fluktuasi atau dispersi dimensi, dan biasanya diukur dengan standar deviasi . Penyebab utama ketidakstabilan dimensi adalah kontrol proses yang lemah, yang merupakan kesalahan acak. Akurasi mengacu pada sejauh mana rata-rata aritmatika dari banyak nilai yang diukur menyimpang dari ukuran nominal untuk ukuran tertentu pada casting, yaitu ukuran penyimpangan rata-rata. Untuk pengecoran investasi, alasan utama untuk akurasi dimensi yang buruk adalah penetapan tingkat penyusutan yang tidak tepat selama desain profil, yang merupakan kesalahan sistematis, yang biasanya disesuaikan dengan perbaikan cetakan berulang kali. Ketepatan dimensi (presisi) adalah kombinasi dari dua di atas. Oleh karena itu, untuk meningkatkan akurasi dimensi coran dan memecahkan masalah toleransi ukuran produk, proses tidak hanya harus dikontrol secara ketat untuk mengurangi fluktuasi dimensi, tetapi juga tingkat penyusutan setiap dimensi pengecoran harus ditetapkan dengan benar saat merancang profil. .
Telah diketahui dengan baik bahwa penyusutan total akhir dari pengecoran presisi adalah kombinasi dari cetakan lilin, penyusutan paduan dan sejumlah kecil ekspansi cangkang. Shell membengkak sekitar 0.25%, dan efeknya terbatas. Meskipun laju penyusutan linier paduan seringkali lebih besar daripada cetakan lilin, fluktuasi dimensi yang disebabkan oleh proses pengepresan lilin memiliki dampak yang lebih besar. Untuk mengurangi biaya perbaikan cetakan dan mengurangi fluktuasi ukuran pengecoran, sangat penting untuk mengontrol tingkat penyusutan cetakan lilin.
1. Penyusutan cetakan lilin
Penyusutan cetakan lilin harus diukur setelah ukuran cetakan lilin benar-benar stabil. Hal ini dikarenakan penyusutan cetakan lilin tidak berhenti sepenuhnya setelah cetakan dikeluarkan. Ukuran cetakan lilin terkadang menjadi stabil hanya beberapa hari setelah cetakan dikeluarkan. Namun, sebagian besar penyusutan bahan cetakan pada dasarnya selesai dalam waktu satu hingga beberapa jam setelah cetakan dikeluarkan. Tingkat penyusutan cetakan lilin terutama memiliki faktor-faktor yang mempengaruhi berikut:
(1) Jenis bahan cetakan;
(2) Ukuran potongan model lilin;
Perlu ditekankan bahwa ukuran penampang cetakan lilin memiliki pengaruh yang signifikan terhadap tingkat penyusutan. Misalnya, tingkat penyusutan bahan cetakan yang tidak terisi khas saat menekan cetakan lilin dengan ketebalan yang berbeda. Ketebalan bagian cetakan lilin umumnya tidak boleh melebihi 13mm. Ketika ketebalan lebih besar dari 13mm, ketebalan dinding dapat dikurangi dengan menggunakan blok lilin dingin atau inti logam untuk mencapai tujuan mengurangi penyusutan, yang sangat penting untuk bahan cetakan non-pengisi.
Catatan: 1. Tingkat penyusutan bahan cetakan yang larut dalam air adalah sekitar 0.25%;
2. Saat menggunakan inti larut, inti keramik, atau tabung kaca kuarsa, tidak ada penyusutan linier dari cetakan lilin yang bersentuhan dengan inti;
(3) Jenis inti
Ukuran rongga cetakan lilin tidak diragukan lagi konsisten dengan bentuk inti. Oleh karena itu, penggunaan core telah menjadi cara untuk meningkatkan akurasi dimensi rongga cetakan lilin.
2. Penyusutan paduan
Penyusutan paduan terutama tergantung pada faktor-faktor berikut:
· Jenis paduan cor dan komposisi kimia;
· Geometri pengecoran (termasuk keadaan kendala dan ukuran bagian);
· Parameter pengecoran, seperti suhu penuangan, suhu cangkang, laju pendinginan pengecoran, dll .;
· Penggunaan inti keramik, tabung kaca kuarsa, dll.
Karena suhu penuangan, suhu cangkang, laju pendinginan pengecoran dan parameter proses lainnya umumnya dikontrol secara ketat oleh kartu proses standar selama proses produksi, fluktuasi ukuran yang disebabkan oleh ini tidak besar antara batch produksi yang berbeda. Bahkan jika suhu penuangan melebihi kisaran yang disyaratkan oleh spesifikasi proses, fluktuasi ukuran pengecoran biasanya tidak besar. Mirip dengan cetakan lilin, ukuran bagian pengecoran dan batasan cangkang cetakan adalah faktor utama yang mempengaruhi penyusutan paduan. Pengalaman menunjukkan bahwa tingkat penyusutan dari ukuran yang sepenuhnya dibatasi adalah 85% hingga 89% dari tingkat penyusutan gratis; ukuran semi-terkendala adalah 94% hingga 95%.
3. Jumlah minimum sampel pertama untuk pengukuran
Tingkat penyusutan yang tercantum di atas adalah data empiris berdasarkan pengalaman masa lalu, bukan tingkat penyusutan yang sebenarnya. Desain dan pembuatan cetakan sesuai dengan data ini, perbaikan tidak bisa dihindari. Untuk meningkatkan akurasi dan tingkat keberhasilan perbaikan, dan mengurangi jumlah perbaikan, kunci utamanya adalah memeriksa dengan cermat ukuran sampel uji coba dalam jumlah yang cukup. Karena ukuran coran yang kami hasilkan tidak bisa sama persis, maka hanya bila jumlah sampel yang diukur cukup besar, maka nilai rata-rata yang diperoleh bisa mendekati rata-rata aritmatika yang sebenarnya. Dari sini, tidak sulit untuk melihat bahwa jumlah minimum sampel pengukuran berhubungan langsung dengan kemampuan proses proses produksi untuk mengontrol konsistensi ukuran produk (Process Capability). Jika coran benar-benar berukuran sama, maka hanya satu sampel yang diperlukan untuk diuji; Sebaliknya, jika ukuran casting sangat berfluktuasi,
Perlu dilakukan pengukuran sampel yang banyak untuk mendapatkan data penyusutan yang lebih akurat. Seperti disebutkan sebelumnya, kemampuan proses produksi untuk mengontrol ukuran dapat diwakili oleh 6σ dari ukuran casting yang dihasilkan oleh proses ini. Dari tingkat teknologi saat ini sebagian besar pengecoran investasi, Hp sebagian besar di atas 0.5, sehingga batch pertama sampel pengukuran umumnya membutuhkan setidaknya 11 sampel.
tiga. Analisis sistem pengukuran
Saat menganalisis dan memecahkan masalah ukuran produk, kita harus memperhatikan keakuratan dan keandalan sistem pengukuran yang digunakan. Selain seringnya kalibrasi alat ukur dan peralatan itu sendiri, juga penting untuk meminimalkan kesalahan pengukuran. Jika sistem pengukuran (termasuk operator dan metode operasi) memiliki kesalahan besar, tidak hanya produk yang ditolak dapat dinilai sebagai produk yang memenuhi syarat, tetapi juga banyak produk yang memenuhi syarat dapat salah dinilai sebagai produk yang ditolak, yang keduanya dapat menyebabkan kecelakaan besar atau biaya ekonomis yang tidak perlu. kerugian. Cara termudah untuk menentukan apakah sistem pengukuran cocok untuk tugas pengukuran tertentu adalah dengan melakukan uji kualifikasi reproduktifitas dan pengulangan. Yang disebut pengulangan berarti bahwa pemeriksa yang sama menggunakan instrumen (atau peralatan) dan metode yang sama untuk memeriksa bagian yang sama dan memperoleh konsistensi hasil. Reproduksibilitas mengacu pada konsistensi hasil yang diperoleh oleh operator yang berbeda menggunakan instrumen yang berbeda untuk memeriksa bagian yang sama. American Automotive Industry Action Group (Automotive Industry Action Group) menetapkan bahwa persentase deviasi standar terintegrasi dari pengulangan dan reproduktifitas R&R dalam deviasi standar fluktuasi ukuran casting yang diukur adalah 30% sebagai standar untuk sistem pengukuran untuk memenuhi persyaratan [5]. Dalam pengukuran beberapa coran berukuran besar dan berbentuk kompleks, tidak semua sistem pengukuran dapat memenuhi persyaratan ini. Kesalahan pengukuran yang diizinkan saat mengukur cetakan harus lebih kecil, biasanya 1/3.
empat. Struktur cetakan dan tingkat pemrosesan
Telah diketahui dengan baik bahwa struktur cetakan dan kualitas pemrosesan memiliki pengaruh penting pada ukuran dan geometri cetakan lilin. Misalnya, apakah mekanisme pemosisian dan penjepitan akurat dan andal, apakah jarak bebas yang cocok dari bagian bergerak (seperti balok bergerak, baut, dll.) sesuai, apakah metode menggambar bermanfaat untuk memastikan akurasi dimensi coran. , dll. Tak perlu dikatakan, untuk sejumlah besar pabrik pengecoran investasi dalam negeri, tingkat desain cetakan dan manufaktur masih perlu segera ditingkatkan.
Lima. Kesimpulannya
Dari analisis di atas, tidak sulit untuk melihat bahwa meningkatkan akurasi dimensi pengecoran investasi adalah proyek sistematis yang melibatkan semua aspek proses produksi pengecoran investasi. Poin-poin utama dapat diringkas sebagai berikut:
1) Ketat mengontrol parameter proses pencetakan, terutama parameter yang memiliki dampak signifikan pada ukuran casting.
2) Pilih bahan cangkang yang sesuai.
3) Mengumpulkan, menghitung dan menganalisis data yang berkaitan dengan penyusutan dengan metode yang benar yang sesuai dengan prinsip-prinsip statistik untuk meningkatkan akurasi tugas penyusutan.
4) Sering memantau sistem pengukuran (termasuk peralatan, personel inspeksi dan teknologi) untuk memastikan bahwa kesalahan pengulangan dan pengulangan memenuhi persyaratan yang ditentukan.
5) Terus meningkatkan tingkat desain dan manufaktur cetakan.
6) Langkah-langkah seperti koreksi casting dan perlakuan panas stabilisasi masih sangat diperlukan dalam banyak kesempatan
Harap simpan sumber dan alamat artikel ini untuk dicetak ulang: Berbagai faktor yang mempengaruhi stabilitas dimensi coran investasi
Minghe Perusahaan Die Casting didedikasikan untuk memproduksi dan menyediakan Suku Cadang Pengecoran berkualitas dan berkinerja tinggi (kisaran suku cadang die casting logam terutama meliputi: Pengecoran Die Dinding Tipis,Die Casting Kamar Panas,Die Casting Ruang Dingin), Layanan Bulat (Layanan Die Casting,Mesin Cnc,Pembuatan cetakan, Perawatan Permukaan). Setiap pengecoran aluminium kustom, magnesium atau Zamak / seng die casting dan persyaratan coran lainnya dipersilakan untuk menghubungi kami.
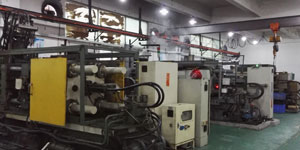
Di bawah kendali ISO9001 dan TS 16949, Semua proses dilakukan melalui ratusan mesin die casting canggih, mesin 5-sumbu, dan fasilitas lainnya, mulai dari blaster hingga mesin cuci Ultra Sonic.Minghe tidak hanya memiliki peralatan canggih tetapi juga profesional tim insinyur berpengalaman, operator dan inspektur untuk membuat desain pelanggan menjadi kenyataan.
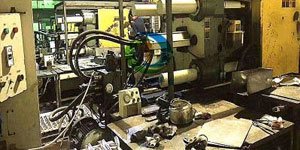
Produsen kontrak die casting. Kemampuannya termasuk bagian die casting aluminium ruang dingin mulai dari 0.15 lbs. hingga 6 lbs., pengaturan perubahan cepat, dan pemesinan. Layanan bernilai tambah termasuk pemolesan, penggetaran, penghalusan, peledakan tembakan, pengecatan, pelapisan, pelapisan, perakitan, dan perkakas. Bahan yang dikerjakan termasuk paduan seperti 360, 380, 383, dan 413.
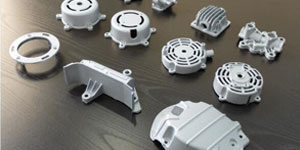
Bantuan desain die casting seng / layanan rekayasa serentak. Produsen kustom pengecoran mati seng presisi. Pengecoran miniatur, coran die tekanan tinggi, coran cetakan multi-slide, coran cetakan konvensional, die unit dan die casting independen dan coran tertutup rongga dapat diproduksi. Pengecoran dapat diproduksi dengan panjang dan lebar hingga 24 inci dalam toleransi +/-0.0005 inci.
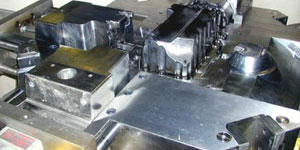
Produsen magnesium die cast bersertifikat ISO 9001: 2015, Kemampuan termasuk die casting magnesium bertekanan tinggi hingga 200 ton ruang panas & 3000 ton ruang dingin, desain perkakas, pemolesan, pencetakan, permesinan, pengecatan bubuk & cair, QA penuh dengan kemampuan CMM , perakitan, pengemasan & pengiriman.
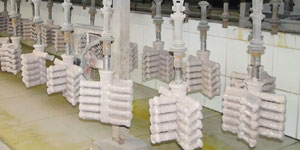
bersertifikat ITAF16949. Layanan Pengecoran Tambahan Termasuk pemilihan investasi,pengecoran pasir,Pengecoran gravitasi, Pengecoran Busa Hilang,Pengecoran Sentrifugal,Pengecoran Vakum,Pengecoran Cetakan Permanen,. Kemampuan termasuk EDI, bantuan teknik, pemodelan solid dan pemrosesan sekunder.
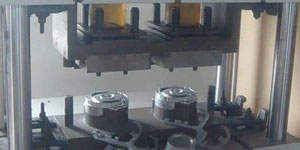
Industri Pengecoran Studi Kasus Suku Cadang untuk: Mobil, Sepeda, Pesawat Terbang, Alat Musik, Perahu, Perangkat Optik, Sensor, Model, Perangkat Elektronik, Penutup, Jam, Mesin, Mesin, Furnitur, Perhiasan, Jig, Telekomunikasi, Pencahayaan, Perangkat Medis, Perangkat Fotografi, Robot, Patung, Peralatan Suara, Peralatan Olahraga, Perkakas, Mainan, dan lainnya.
Apa yang dapat kami bantu untuk Anda lakukan selanjutnya?
Pergi Ke Beranda Untuk Die Casting Cina
→Bagian casting-Cari tahu apa yang telah kita lakukan.
→Tips Terkait Tentang Layanan Die Casting
By Produsen Die Casting Minghe |Kategori: Artikel Bermanfaat |Bahan Tags: Pengecoran Aluminium, Pengecoran Seng, Pengecoran Magnesium, Pengecoran Titanium, Pengecoran Stainless Steel, Pengecoran Kuningan,Pengecoran Perunggu,Video Transmisi,sejarah perusahaan,Aluminium Die Casting |Komentar Dinonaktifkan