Tindakan Pencegahan Untuk Pengecoran Pasir Kaca Air
Apa faktor yang mempengaruhi "penuaan" gelas air? Bagaimana cara menghilangkan "penuaan" gelas air?
Gelas air yang baru disiapkan adalah solusi yang tepat. Namun selama proses penyimpanan, asam silikat dalam gelas air akan mengalami polimerisasi kondensasi, yang secara bertahap akan polikondensat dari larutan sejati menjadi larutan asam silikat makromolekul dan akhirnya menjadi gel asam silikat. Oleh karena itu, gelas air sebenarnya adalah campuran heterogen yang terdiri dari asam polisilat dengan derajat polimerisasi yang berbeda, yang mudah dipengaruhi oleh modulus, konsentrasi, suhu, kandungan elektrolit, dan waktu penyimpanannya.
Selama penyimpanan, molekul gelas air mengalami polimerisasi kondensasi untuk membentuk gel, dan kekuatan ikatannya secara bertahap menurun dengan perpanjangan waktu penyimpanan. Fenomena ini disebut "penuaan" gelas air.
Fenomena "penuaan" dapat dijelaskan dengan dua set data uji berikut: gelas air modulus tinggi (M=2.89, =1.44g/cm3) setelah penyimpanan 20, 60, 120, 180, 240 hari, CO2 mengeras gelas air ditiup Kekuatan tarik kering pasir turun masing-masing sebesar 9.9%, 14%, 23.5%, 36.8% dan 40%; natrium silikat modulus rendah (M=2.44, =1.41g/cm3) disimpan selama 7, 30, 60 dan 90 hari setelah dikeringkan. Kekuatan tarik menurun masing-masing sebesar 4.5%, 5%, 7.3% dan 11%.
Waktu penyimpanan gelas air memiliki pengaruh yang kecil terhadap kekuatan awal pasir pengerasan gelas air yang dikeraskan secara ester, tetapi memiliki pengaruh yang signifikan terhadap kekuatan selanjutnya. Menurut pengukuran, itu berkurang sekitar 60% untuk gelas air modulus tinggi, dan 15-20% untuk gelas air modulus rendah. . Kekuatan sisa juga menurun dengan perpanjangan waktu penyimpanan.
Selama penyimpanan gelas air, polikondensasi dan depolimerisasi asam polisilik berlangsung pada saat yang sama, berat molekul tidak proporsional, dan akhirnya sistem multi-dispersi di mana asam monoortosilikat dan partikel koloid terbentuk. Artinya, selama proses penuaan gelas air, Derajat polimerisasi asam silikat tidak proporsional, dan kandungan asam monoortosilikat dan asam polisilat tinggi meningkat seiring dengan perpanjangan waktu penyimpanan. Sebagai hasil dari reaksi polimerisasi kondensasi dan depolimerisasi gelas air selama penyimpanan, kekuatan ikatan berkurang, yaitu, fenomena "penuaan" terjadi.
Faktor utama yang mempengaruhi "penuaan" gelas air adalah: waktu penyimpanan, modulus dan konsentrasi gelas air. Semakin lama waktu penyimpanan, semakin tinggi modulus dan semakin besar konsentrasi, semakin serius "penuaan".
Gelas air yang sudah lama ada dapat dimodifikasi dengan berbagai cara untuk menghilangkan "penuaan" dan mengembalikan gelas air ke kinerja gelas air tawar:
1. Modifikasi fisik
Penuaan gelas air adalah proses spontan yang secara perlahan melepaskan energi. Modifikasi fisik gelas air "tua" adalah dengan menggunakan medan magnet, ultrasound, frekuensi tinggi atau pemanasan untuk memberikan energi ke sistem gelas air dan mempromosikan polimerisasi tinggi lem polisilikat. Partikel mendepolimerisasi ulang dan mempromosikan homogenisasi berat molekul asam polisilicic, sehingga menghilangkan fenomena penuaan, yang merupakan mekanisme modifikasi fisik. Misalnya, setelah perlakuan dengan medan magnet, kekuatan pasir natrium silikat meningkat 20-30%, jumlah natrium silikat yang ditambahkan berkurang 30-40%, CO2 disimpan, kolapsbilitas ditingkatkan, dan ada yang baik. manfaat ekonomi.
Kerugian dari modifikasi fisik adalah tidak tahan lama, dan kekuatan rekat akan berkurang bila disimpan setelah perlakuan, sehingga sangat cocok untuk digunakan sesegera mungkin setelah perlakuan di pengecoran. Khusus untuk gelas air dengan M>2.6, konsentrasi molekul asam silikat besar, dan setelah modifikasi fisik dan depolimerisasi, polikondensat relatif cepat. Yang terbaik adalah menggunakannya segera setelah perawatan.
2. Modifikasi kimia
Modifikasi kimia adalah dengan menambahkan sejumlah kecil senyawa ke dalam gelas air, senyawa ini semua mengandung karboksil, amida, karbonil, hidroksil, eter, amino dan gugus polar lainnya, yang teradsorpsi pada molekul asam silikat atau partikel koloid melalui ikatan hidrogen atau statis. listrik. Permukaan, mengubah energi potensial permukaan dan kemampuan solvasi, meningkatkan stabilitas asam polisilicic, sehingga mencegah "penuaan" dari melanjutkan.
Misalnya, menambahkan poliakrilamida, pati termodifikasi, polifosfat, dll. ke gelas air dapat mencapai hasil yang lebih baik.
Memasukkan bahan organik ke dalam gelas air biasa atau bahkan gelas air yang dimodifikasi dapat memainkan berbagai fungsi, seperti: mengubah sifat aliran kental gelas air; meningkatkan kinerja pemodelan campuran gelas air; meningkatkan kekuatan ikatan untuk membuat gelas air benar-benar ditambahkan Jumlahnya berkurang; plastisitas gel asam silikat ditingkatkan; kekuatan sisa berkurang, sehingga pasir gelas air lebih cocok untuk besi cor dan paduan non-ferrous.
3. Modifikasi fisika-kimia
Modifikasi fisik cocok untuk gelas air "tua", dan dapat digunakan segera setelah modifikasi. Modifikasi kimia cocok untuk memproses gelas air tawar, dan gelas air yang dimodifikasi dapat disimpan untuk waktu yang lama. Kombinasi modifikasi fisik dan modifikasi kimia dapat membuat gelas air memiliki efek modifikasi yang tahan lama. Misalnya, menambahkan poliakrilamida ke autoklaf untuk memodifikasi gelas air "penuaan" memiliki efek yang baik. Di antara mereka, tekanan dan tekanan autoklaf digunakan. Pengadukan adalah modifikasi fisik, dan penambahan poliakrilamida adalah modifikasi kimia.
Bagaimana mencegah CO2 meniup permukaan cetakan pasir (inti) natrium silikat yang mengeras?
Setelah pasir soda natrium silikat ditiup CO2 mengeras dan dibiarkan untuk jangka waktu tertentu, kadang-kadang zat seperti embun beku akan muncul di permukaan cetakan bawah (inti), yang secara serius akan mengurangi kekuatan permukaan tempat dan dengan mudah menghasilkan pasir cacat pencucian selama penuangan. Menurut analisis, komponen utama zat putih ini adalah NaHCO3, yang mungkin disebabkan oleh kelembaban atau CO2 yang berlebihan pada pasir natrium silikat. Reaksinya adalah sebagai berikut:
- Na2CO3+H2O→NaHCO3+NaOH
- Na2O+2CO2+H2O→2NaHCO3
- NaHCO3 dengan mudah bermigrasi keluar dengan uap air, menyebabkan seperti embun beku pada permukaan cetakan dan inti.
Solusinya adalah sebagai berikut:
- Kontrol kadar air pasir natrium silikat agar tidak terlalu tinggi (terutama pada musim hujan dan musim dingin).
- Waktu untuk meniup CO2 tidak boleh terlalu lama.
- Cetakan dan inti yang mengeras tidak boleh ditempatkan untuk waktu yang lama, dan harus dicetak dan dituang tepat waktu.
- Menambahkan sekitar 1% (fraksi massa) sirup dengan kepadatan 1.3g/cm3 ke pasir natrium silikat dapat secara efektif mencegah permukaan menjadi bubuk.
Bagaimana cara meningkatkan ketahanan penyerapan air dari cetakan pasir kaca air (inti)?
Inti pasir kaca air soda yang dikeraskan dengan metode CO2 atau pemanasan dirakit dalam cetakan tanah liat basah. Jika tidak dituangkan tepat waktu, kekuatan inti pasir akan berkurang tajam, tidak hanya dapat merayap, bahkan runtuh; itu disimpan di lingkungan yang lembab. Kekuatan inti pasir juga berkurang secara signifikan. Tabel 1 menunjukkan nilai kekuatan CO2 hardened sodium water glass sand core ketika ditempatkan di lingkungan dengan kelembaban relatif 97% selama 24 jam. Alasan hilangnya kekuatan saat disimpan di lingkungan yang lembab adalah karena hidrasi ulang gelas air natrium. Na+ dan OH— dalam matriks pengikat natrium silikat menyerap kelembaban dan mengikis matriks, akhirnya memutuskan ikatan silikon-oksigen Si—O—Si, menghasilkan penurunan kekuatan ikatan pasir natrium silikat yang signifikan.
Langkah-langkah untuk mengatasi masalah ini adalah:
- 1. Gelas air lithium ditambahkan ke gelas air natrium, atau Li2CO3, CaCO3, ZnCO3 dan aditif anorganik lainnya ditambahkan ke gelas air natrium, karena karbonat dan silikat yang relatif tidak larut dapat terbentuk, dan ion natrium bebas dapat dikurangi Oleh karena itu, kelembaban resistensi penyerapan pengikat gelas air natrium dapat ditingkatkan.
- 2. Tambahkan sedikit bahan organik atau bahan organik dengan fungsi surfaktan ke dalam gelas air natrium. Ketika pengikat mengeras, ion Na+ dan OH- hidrofilik dalam gel gelas air natrium dapat digantikan oleh gugus hidrofobik organik, atau Dikombinasikan satu sama lain, basa hidrofobik organik yang terpapar meningkatkan penyerapan air.
- 3. Meningkatkan modulus gelas air, karena ketahanan kelembaban gelas air modulus tinggi lebih kuat daripada gelas air modulus rendah.
- 4. Tambahkan hidrolisat pati ke pasir natrium silikat. Metode yang lebih baik adalah dengan menggunakan hidrolisat pati untuk memodifikasi gelas air natrium.
4 Apa karakteristik proses komposit pasir resin fenolik kaca-alkali air yang dihembuskan CO2?
Dalam beberapa tahun terakhir, untuk meningkatkan kualitas coran baja, beberapa perusahaan kecil dan menengah sangat perlu mengadopsi proses pasir resin. Namun, karena kapasitas ekonomi yang terbatas, mereka tidak dapat membeli peralatan regenerasi pasir resin, dan pasir lama tidak dapat didaur ulang dan digunakan kembali, sehingga mengakibatkan biaya produksi yang tinggi. Untuk menemukan cara yang efektif untuk meningkatkan kualitas coran tanpa meningkatkan biaya terlalu banyak, karakteristik proses dari CO2 meniup pasir natrium silikat yang mengeras dan CO2 yang meniup pasir resin fenolik alkali yang dikeraskan dapat digabungkan, dan CO2 yang meniup natrium silikat yang mengeras—basa resin fenolik dapat digunakan. Proses peracikan pasir resin menggunakan pasir resin alkaline phenolic sebagai pasir permukaan dan pasir water glass sebagai pasir belakang, sedangkan blowing CO2 untuk pengerasan.
Resin fenolik yang digunakan dalam pasir resin fenolik alkali CO2 dibuat dengan polikondensasi fenol dan formaldehida di bawah aksi katalis basa kuat dan menambahkan zat penghubung. Nilai PH-nya adalah 13, dan viskositasnya adalah 500mPa•s. Jumlah resin fenolik yang ditambahkan ke pasir adalah 3% sampai 4% (fraksi massa). Ketika laju aliran CO2 adalah 0.8~1.0m3/jam, waktu tiupan terbaik adalah 30~60 detik; jika waktu bertiup terlalu pendek, kekuatan pengerasan inti pasir akan rendah; jika waktu bertiup terlalu lama, kekuatan inti pasir tidak akan meningkat, dan itu adalah gas yang terbuang.
CO2—pasir resin alkali fenolik tidak mengandung unsur-unsur berbahaya seperti N, P, S, dll., sehingga cacat pengecoran seperti pori-pori, retakan mikro permukaan, dll. yang disebabkan oleh unsur-unsur ini dihilangkan; gas berbahaya seperti H2S dan SO2 tidak dilepaskan selama penuangan, yang bermanfaat bagi perlindungan lingkungan; Collapibility yang baik, mudah dibersihkan; akurasi dimensi tinggi; efisiensi produksi yang tinggi.
Proses komposit pasir resin fenolik kaca-alkali air yang dihembuskan CO2 dapat digunakan secara luas dalam coran baja, coran besi, paduan tembaga dan coran paduan ringan.
Proses komposit adalah proses yang sederhana dan nyaman. Prosesnya adalah sebagai berikut: pertama campur pasir resin dan pasir natrium silikat secara terpisah, lalu masukkan ke dalam dua ember pasir; kemudian tambahkan pasir resin campuran sebagai pasir permukaan ke dalam kotak pasir Dan pon, ketebalan lapisan pasir permukaan umumnya 30-50mm; kemudian pasir gelas air ditambahkan untuk membuat pasir belakang terisi dan padat; akhirnya, gas CO2 ditiup ke dalam cetakan untuk pengerasan.
Diameter tabung peniup umumnya 25mm, dan kisaran pengerasan sekitar 6 kali diameter tabung peniup.
Waktu peniupan tergantung pada ukuran, bentuk, aliran gas, dan luas sumbat buangan cetakan pasir (inti). Umumnya, waktu bertiup dikontrol dalam waktu 15 ~ 40 detik.
Setelah meniup cetakan pasir keras (inti), cetakan dapat diambil. Kekuatan cetakan pasir (inti) meningkat dengan cepat. Sikat cat dalam waktu setengah jam setelah mengambil cetakan, dan tutup kotak untuk menuangkan setelah 4 jam.
Proses komposit sangat cocok untuk pabrik pengecoran baja yang tidak memiliki peralatan regenerasi pasir resin dan perlu menghasilkan coran berkualitas tinggi. Prosesnya sederhana dan mudah dikendalikan, dan kualitas coran yang dihasilkan setara dengan coran pasir resin lainnya.
CO2 meniup pasir natrium silikat mengeras juga dapat diperparah dengan CO2 meniup pasir resin natrium poliakrilat mengeras untuk produksi berbagai coran berkualitas tinggi.
Apa pro dan kontra dari proses pengerasan pasir natrium silikat komposit ester CO2-organik?
Dalam beberapa tahun terakhir, proses pasir natrium silikat komposit ester CO2-organik memiliki tren aplikasi yang berkembang. Prosesnya adalah sebagai berikut: tambahkan sejumlah ester organik selama pencampuran pasir (biasanya setengah dari jumlah normal yang dibutuhkan atau 4~6% dari berat gelas air); setelah pemodelan selesai, tiup CO2 untuk mengeraskan kekuatan pelepasan cetakan (ketahanan tekan umumnya diperlukan) Kekuatannya sekitar 0.5MPa); setelah pembongkaran, ester organik terus mengeras, dan kekuatan pasir cetakan meningkat lebih cepat; setelah CO2 ditiup dan ditempatkan selama 3 ~ 6 jam, cetakan pasir dapat digabungkan dan dituangkan.
Mekanisme pengerasannya adalah:
Ketika pasir kaca air meniup CO2, di bawah aksi perbedaan tekanan gas dan perbedaan konsentrasi, gas CO2 akan mencoba mengalir ke segala arah pasir cetakan. Setelah gas CO2 kontak dengan gelas air, ia segera bereaksi dengannya membentuk gel. Karena efek difusi, reaksi selalu dari luar ke dalam, dan lapisan luar pertama-tama membentuk film gel, yang mencegah gas CO2 dan gelas air untuk terus bereaksi. Oleh karena itu, dalam waktu singkat, apapun metode yang digunakan untuk mengendalikan gas CO2, tidak mungkin membuatnya bereaksi dengan semua gelas air. Menurut analisis, ketika pasir cetak mencapai kekuatan tiupan terbaik, gelas air yang bereaksi dengan gas CO2 adalah sekitar 65%. Ini berarti bahwa gelas air tidak sepenuhnya memberikan efek ikatannya, dan setidaknya 35% gelas air tidak bereaksi. Pengeras ester organik dapat membentuk campuran yang seragam dengan pengikat, dan dapat memberikan permainan penuh pada efek ikatan pengikat. Semua bagian pasir inti membangun kekuatan pada kecepatan yang sama.
Menambah jumlah water glass yang ditambahkan akan meningkatkan kekuatan akhir cetakan pasir, tetapi kekuatan sisa juga akan meningkat, sehingga sulit untuk membersihkan pasir. Ketika jumlah gelas air yang ditambahkan terlalu kecil, kekuatan akhir terlalu kecil dan tidak dapat memenuhi persyaratan untuk digunakan. Dalam produksi aktual, jumlah gelas air yang ditambahkan umumnya dikontrol sekitar 4%.
Saat menggunakan ester organik saja untuk mengeras, jumlah umum ester organik yang ditambahkan adalah 8-15% dari jumlah gelas air. Saat menggunakan pengerasan komposit, diperkirakan sekitar setengah gelas air telah mengeras ketika CO2 ditiup, dan sekitar setengah gelas air belum mengeras. Oleh karena itu, jumlah ester organik lebih tepat untuk mencapai 4 sampai 6% dari jumlah gelas air.
Metode pengerasan komposit dapat memberikan permainan penuh pada keuntungan ganda pengerasan CO2 dan pengerasan ester organik, dan dapat sepenuhnya mengerahkan efek ikatan gelas air untuk mencapai kecepatan pengerasan yang cepat, pelepasan cetakan awal, kekuatan tinggi, kolapsbilitas yang baik, dan biaya rendah. Efek yang komprehensif.
Namun, proses pengerasan komposit ester CO2-organik perlu menambahkan 0.5 hingga 1% lebih banyak gelas air daripada metode pengerasan ester organik sederhana, yang akan meningkatkan kesulitan regenerasi pasir gelas air bekas.
Mengapa pasir lengket mudah dihasilkan ketika proses pasir natrium silikat digunakan untuk menghasilkan coran besi? Bagaimana mencegahnya?
Ketika cetakan pasir (inti) yang terbuat dari pasir natrium silikat digunakan untuk menuangkan besi tuang, pasir lengket yang serius sering dihasilkan, yang membatasi penerapannya dalam produksi besi tuang.
Na2O, SiO2 dalam pasir natrium silikat dan oksida besi yang dihasilkan oleh logam cair selama penuangan membentuk silikat dengan titik leleh rendah. Seperti disebutkan sebelumnya, jika senyawa ini mengandung lebih banyak kaca amorf yang dapat melebur, gaya ikatan antara lapisan kaca ini dan permukaan tuangan sangat kecil, dan koefisien susutnya berbeda dari logam. Tegangan besar mudah dihilangkan dari permukaan coran tanpa pasir yang menempel. Jika senyawa yang terbentuk pada permukaan pengecoran memiliki kandungan SiO2 yang tinggi dan kandungan FeO, MnO, dll yang rendah, strukturnya yang padat pada dasarnya memiliki struktur kristal, yang akan digabungkan dengan kuat dengan pengecoran, menghasilkan pasir yang lengket. .
Ketika pasir natrium silikat digunakan untuk menghasilkan coran besi, karena suhu penuangan yang rendah dan kandungan karbon yang tinggi dari coran besi, besi dan mangan tidak mudah teroksidasi, dan lapisan pasir lengket yang dihasilkan memiliki struktur kristal, dan sulit untuk membentuk lapisan yang cocok antara coran besi dan lapisan pasir lengket. Ketebalan lapisan oksida besi berbeda dari pasir resin antara pengecoran dan lapisan pasir lengket, yang dapat menghasilkan film karbon cerah melalui pirolisis resin saat memproduksi coran besi, sehingga lapisan pasir lengket tidak mudah dihilangkan.
Untuk mencegah produksi pasir gelas air soda dari produksi coran besi, pelapis yang sesuai dapat digunakan. Seperti cat berbasis air, permukaannya perlu dikeringkan setelah dicat, jadi cat cepat kering berbasis alkohol adalah yang terbaik.
Secara umum, pengecoran besi juga dapat menambahkan bubuk batubara dalam jumlah yang sesuai (seperti 3% hingga 6%) (fraksi massa) ke pasir natrium silikat, sehingga pirolisis bubuk batubara antara pengecoran dan lapisan pasir dapat menghasilkan film karbon yang cerah. Itu tidak dibasahi oleh logam dan oksidanya, sehingga lapisan pasir yang lengket mudah terkelupas dari casting.
Apakah pasir natrium silikat diharapkan menjadi pasir cetak yang ramah lingkungan tanpa pembuangan limbah pasir?
Gelas air tidak berwarna, tidak berbau, dan tidak beracun. Ini tidak akan menimbulkan masalah serius jika menyentuh kulit dan pakaian dan bilas dengan air, tetapi harus dihindari untuk memercik ke mata. Gelas air tidak memiliki gas yang mengiritasi atau berbahaya yang dilepaskan selama pencampuran pasir, pemodelan, pengerasan dan penuangan, dan tidak ada polusi hitam dan asam. Namun, jika prosesnya tidak tepat dan terlalu banyak natrium silikat ditambahkan, kolapsitas pasir natrium silikat tidak akan baik, dan debu akan beterbangan selama pembersihan pasir, yang juga akan menyebabkan polusi. Pada saat yang sama, sulit untuk meregenerasi pasir tua, dan pembuangan limbah pasir menyebabkan polusi alkali ke lingkungan.
Jika kedua masalah ini dapat diatasi, pasir natrium silikat dapat menjadi pasir cetak yang ramah lingkungan dan pada dasarnya tidak membuang limbah pasir.
Langkah mendasar untuk memecahkan dua masalah ini adalah mengurangi jumlah gelas air yang ditambahkan menjadi kurang dari 2%, yang pada dasarnya dapat menghilangkan pasir. Ketika jumlah gelas air yang ditambahkan berkurang, sisa Na2O di pasir lama juga berkurang. Dengan menggunakan metode regenerasi kering yang relatif sederhana, dimungkinkan untuk mempertahankan sisa Na2O dalam pasir yang bersirkulasi di bawah 0.25%. Pasir reklamasi ini dapat memenuhi persyaratan aplikasi pasir cetakan tunggal untuk coran baja kecil dan menengah. Pada saat ini, bahkan jika pasir natrium silikat tua tidak menggunakan metode basah yang mahal dan rumit untuk regenerasi, tetapi metode kering yang relatif sederhana dan murah digunakan, dapat sepenuhnya didaur ulang, pada dasarnya tidak ada pasir limbah yang dibuang, dan rasionya pasir menjadi besi Dapat dikurangi menjadi kurang dari 1:1.
Bagaimana cara meregenerasi pasir natrium silikat secara efektif?
Jika sisa Na2O di pasir natrium silikat lama terlalu tinggi, setelah menambahkan natrium silikat ke pasir, pasir cetak tidak akan memiliki cukup waktu yang dapat digunakan, dan akumulasi terlalu banyak Na2O akan menurunkan sifat tahan api pasir kuarsa. Oleh karena itu, sisa Na2O harus dihilangkan sebanyak mungkin saat meregenerasi pasir natrium silikat bekas.
Harap simpan sumber dan alamat artikel ini untuk dicetak ulang: Tindakan Pencegahan Untuk Pengecoran Pasir Kaca Air
Minghe Perusahaan Die Casting didedikasikan untuk memproduksi dan menyediakan Suku Cadang Pengecoran berkualitas dan berkinerja tinggi (kisaran suku cadang die casting logam terutama meliputi: Pengecoran Die Dinding Tipis,Die Casting Kamar Panas,Die Casting Ruang Dingin), Layanan Bulat (Layanan Die Casting,Mesin Cnc,Pembuatan cetakan, Perawatan Permukaan). Setiap pengecoran aluminium kustom, magnesium atau Zamak / seng die casting dan persyaratan coran lainnya dipersilakan untuk menghubungi kami.
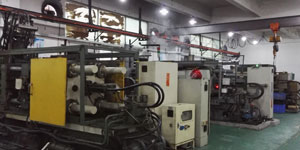
Di bawah kendali ISO9001 dan TS 16949, Semua proses dilakukan melalui ratusan mesin die casting canggih, mesin 5-sumbu, dan fasilitas lainnya, mulai dari blaster hingga mesin cuci Ultra Sonic.Minghe tidak hanya memiliki peralatan canggih tetapi juga profesional tim insinyur berpengalaman, operator dan inspektur untuk membuat desain pelanggan menjadi kenyataan.
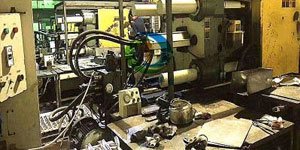
Produsen kontrak die casting. Kemampuannya termasuk bagian die casting aluminium ruang dingin mulai dari 0.15 lbs. hingga 6 lbs., pengaturan perubahan cepat, dan pemesinan. Layanan bernilai tambah termasuk pemolesan, penggetaran, penghalusan, peledakan tembakan, pengecatan, pelapisan, pelapisan, perakitan, dan perkakas. Bahan yang dikerjakan termasuk paduan seperti 360, 380, 383, dan 413.
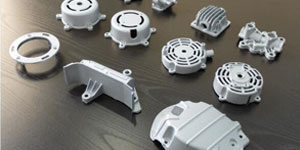
Bantuan desain die casting seng / layanan rekayasa serentak. Produsen kustom pengecoran mati seng presisi. Pengecoran miniatur, coran die tekanan tinggi, coran cetakan multi-slide, coran cetakan konvensional, die unit dan die casting independen dan coran tertutup rongga dapat diproduksi. Pengecoran dapat diproduksi dengan panjang dan lebar hingga 24 inci dalam toleransi +/-0.0005 inci.
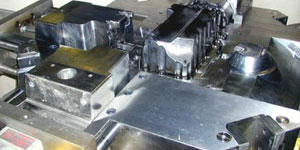
Produsen magnesium die cast bersertifikat ISO 9001: 2015, Kemampuan termasuk die casting magnesium bertekanan tinggi hingga 200 ton ruang panas & 3000 ton ruang dingin, desain perkakas, pemolesan, pencetakan, permesinan, pengecatan bubuk & cair, QA penuh dengan kemampuan CMM , perakitan, pengemasan & pengiriman.
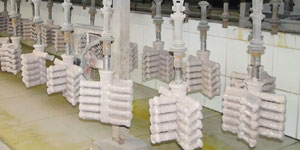
bersertifikat ITAF16949. Layanan Pengecoran Tambahan Termasuk pemilihan investasi,pengecoran pasir,Pengecoran gravitasi, Pengecoran Busa Hilang,Pengecoran Sentrifugal,Pengecoran Vakum,Pengecoran Cetakan Permanen,. Kemampuan termasuk EDI, bantuan teknik, pemodelan solid dan pemrosesan sekunder.
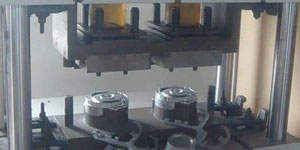
Industri Pengecoran Studi Kasus Suku Cadang untuk: Mobil, Sepeda, Pesawat Terbang, Alat Musik, Perahu, Perangkat Optik, Sensor, Model, Perangkat Elektronik, Penutup, Jam, Mesin, Mesin, Furnitur, Perhiasan, Jig, Telekomunikasi, Pencahayaan, Perangkat Medis, Perangkat Fotografi, Robot, Patung, Peralatan Suara, Peralatan Olahraga, Perkakas, Mainan, dan lainnya.
Apa yang dapat kami bantu untuk Anda lakukan selanjutnya?
Pergi Ke Beranda Untuk Die Casting Cina
→Bagian casting-Cari tahu apa yang telah kita lakukan.
→Tips Terkait Tentang Layanan Die Casting
By Produsen Die Casting Minghe |Kategori: Artikel Bermanfaat |Bahan Tags: Pengecoran Aluminium, Pengecoran Seng, Pengecoran Magnesium, Pengecoran Titanium, Pengecoran Stainless Steel, Pengecoran Kuningan,Pengecoran Perunggu,Video Transmisi,sejarah perusahaan,Aluminium Die Casting |Komentar Dinonaktifkan