Bagaimana memastikan stabilitas sistem pasir hijau?
I. Pendahuluan
Karena perubahan kondisi produksi dan lingkungan, parameter casting lainnya pasti akan berubah. Jika proses pencetakan pasir tidak dapat disesuaikan tepat waktu, sistem pasir akan menjadi tidak stabil, yang pada akhirnya akan menyebabkan pembersihan coran atau bahkan skrap menjadi lebih sulit;
Dengan cara ini, perlu untuk menyesuaikan proses pasir cetakan asli untuk menstabilkan sistem pasir; komposisi bahan pasir cetak terutama terdiri dari pasir tua, pasir mentah, bentonit dan aditif. Karena lebih dari 95% pasir cetakan adalah pasir tua, dan pasir tua dipengaruhi oleh faktor-faktor seperti rasio pasir-besi yang berbeda dari pengecoran dan jumlah pencampuran yang berbeda dari pasir inti, menghasilkan fluktuasi yang sangat besar dalam komposisi bahan. Oleh karena itu, untuk mengontrol komposisi pasir cetak perlu dilakukan pemeriksaan kandungan bentonit efektif, kandungan aditif efektif dan kandungan lumpur pada pasir cetakan untuk menentukan jumlah penambahan bentonit, aditif dan pasir mentah pada saat pencampuran pasir.
Artikel ini akan memperkenalkan secara singkat bagaimana pengecoran perusahaan penulis berakar pada proses produksi yang sebenarnya.
Menurut perubahan parameter, proses pencetakan pasir disesuaikan untuk memastikan stabilitas sistem pasir.
2. Definisi parameter utama pasir cetak:
1. Kandungan bentonit efektif: Kandungan bentonit (aktif) efektif ditentukan berdasarkan karakteristik mineral montmorillonit yang terkandung dalam bentonit yang dapat menyerap metilen biru dan pewarna lainnya; mengacu pada titrasi pasir cetak 5.00g dengan konsentrasi 0.20% larutan metilen biru murni [ mL]; dikonversi sesuai dengan rumus kurva standar bentonit (%)
2. Dosis aditif efektif: Dibandingkan dengan evolusi gas aditif pasir cetak dan dihitung dengan menggunakan rumus; yaitu, evolusi gas 1.00g pasir cetak pada 900 °C [mL] dikurangi evolusi gas dari bentonit aktif dalam pasir cetak (jumlah rata-rata diukur sebelum perhitungan ) Kemudian bandingkan dengan 1g volume gas aditif (%).
3. Kandungan lumpur: Menurut standar nasional GB/T9442-1998, partikel serbuk halus dengan diameter kurang dari 20μm didefinisikan sebagai lumpur. Lumpur biasanya dihilangkan dengan metode pembilasan [2].
4. Ukuran partikel pasir cetakan: dinyatakan dalam kehalusan AFS, yaitu ukuran rata-rata partikel pasir direfleksikan menurut tanda saringan imajiner [3];
5. Metode penghitungan kehalusan AFS: Prosedur pengukuran kehalusan AFS dan metode penghitungan yang ditentukan oleh American Institute of Foundry adalah sebagai berikut:
. Pertama-tama timbang sekitar 50g sampel pasir yang akan diukur, bersihkan lumpurnya, keringkan, lalu diayak
. Timbang dan catat kualitas partikel pasir yang tersisa pada setiap saringan;
. Hitung persentase jumlah partikel pasir yang tersisa pada setiap ayakan terhadap jumlah total sampel pasir;
. Kalikan persentase jumlah partikel pasir yang tersisa di setiap saringan dengan "pengganda kehalusan AFS" yang sesuai dengan setiap saringan;
. Tambahkan produk di atas untuk setiap nomor saringan untuk menemukan jumlah:
. Bagilah jumlah yang diperoleh pada butir 5 dengan jumlah persentase pasir yang tertahan pada setiap ayakan pada butir 3 untuk mendapatkan kehalusan AFS
3. Rencana penyesuaian:
Peralatan pencampur pasir yang digunakan oleh pabrik adalah pabrik pasir DISA dan peralatan cetakan KW garis cetakan tekanan statis; menggunakan statistik data selama setengah tahun, rencana berikut telah dirumuskan untuk sistem pasir cetaknya:
1. Statistik:
Tentukan jumlah pasir cetakan yang ditambahkan ke setiap kotak sesuai dengan nilai pengaturan dari tuan rumah cetakan, dan hitung rasio pasir-besi dari setiap kotak coran sesuai dengan berat setiap kotak coran dan berat penuangan sistem, dan jumlah pasir inti yang digunakan dalam pengecoran;
Statistik jumlah limbah pasir yang dibuang dan penggunaan pasir inti dan bahan penolong
Statistik penghilangan debu dari sistem pasir cetak
2. Penyesuaian pasir:
Menurut situasi produksi, ketika pengecoran terus menerus diproduksi selama dua hari atau lebih, jumlah tambahan aksesori pasir cetak (bentonit, aditif) harus diperbaiki, dan perubahan jumlah efektif pasir cetak harus dihitung, dan kemudian secara bertahap diverifikasi selama produksi terus menerus dari coran lainnya Hubungan antara pasir untuk rasio besi dan jumlah yang ditambahkan;
Penyesuaian ukuran partikel pasir cetakan: sesuaikan dengan nilai median saringan 50/100 (pasir silika saringan 50/100, nilai rata-rata kehalusan rata-rata adalah 50 [4]), ketika AFS pasir cetakan adalah kurang dari atau sama dengan 50, dengan menambahkan pasir halus 70/140 atau pasir baru yang lebih halus 140/70 disesuaikan, 30kg-60kg ditambahkan per mill, dan perubahan ukuran partikel dianalisis.
Penyesuaian kandungan lumpur pasir cetak: analisis perubahan kandungan lumpur sistem pasir cetak melalui statistik penghilangan debu harian;
Keempat, proses penyesuaian khusus:
1. Statistik rasio pengecoran pasir terhadap besi:
(Catatan: Karena badan silinder X2B1 dicetak dengan inti pasir integral, itu tidak akan membakar pasir cetakan, sehingga berat pasir cetakan luar dari pengecoran dihitung sebagai "0")
2. Sesuaikan jumlah efektif sesuai dengan rasio pasir-besi casting. Rasio pasir-besi dari blok silinder 56D adalah 6.57. Di antara coran di atas, rasio pasir-besi adalah yang tertinggi di antara coran blok silinder. Oleh karena itu, blok silinder 56D pertama kali diuji:
Ketika 56D diproduksi selama tiga hari berturut-turut, jumlah aditif adalah 22kg/mill, dan jumlah aditif tanah liat adalah 33kg/mill; jumlah efektif aditif naik dari 4.55% menjadi 5.03%; jumlah efektif tanah liat naik dari 6.56% menjadi 7%; peningkatan sekitar 0.5%; Artinya, ketika silinder 56D diproduksi, jumlah tambahan harus disesuaikan lebih tinggi dari nilai keseimbangan sistem pasir;
Melalui analisis data di atas, jumlah bahan penolong yang ditambahkan disesuaikan sebagai berikut:
1) Ketika silinder direproduksi, jumlah aditif disesuaikan menjadi 19kg/mill, dan ketika jumlah aditif tanah liat adalah 26kg/mill, data statistik selama tiga hari berturut-turut menunjukkan bahwa jumlah efektif aditif telah berubah dari 4.36% menjadi 4.29% ; jumlah efektif tanah liat telah berubah dari 4.36% menjadi 4.29%. 7.22% menjadi 7.11%; jumlah efektif berfluktuasi sebesar 0.1%; oleh karena itu, rencana penyesuaian proses masuk akal dan dapat memastikan keseimbangan sistem pasir cetak;
2) Demikian pula, hubungan antara jumlah bahan pembantu yang ditambahkan ke coran lain dan jumlah efektif dihitung melalui analisis data eksperimen dan teori; ketika mereproduksi coran yang berbeda, sesuaikan jumlah bahan tambahan yang sesuai.
3. Gunakan pasir baru 70/140 mesh dan pasir baru 140/70 untuk menyesuaikan ukuran pasir (kandungan lumpur pasir prototipe adalah 11.42%):
Dari 16 Januari hingga 21 Januari, total 4257 kali penggilingan pasir dalam lima hari, sekitar 4257*3/900=14 kali; ukuran partikel setiap siklus berubah sekitar 0.26 (per penggilingan); maka pasir cetakan pada tanggal 16 Januari Nilai AFS adalah 49.15; mulai 16 Januari, lima hari penambahan terus menerus 70/140 pasir baru untuk menyesuaikan ukuran partikel, 60kg per penggilingan, nilai AFS pasir cetak pada 21 Januari adalah 52.84;
Dari 25 Januari hingga 27 Januari, total 2165 kali penggilingan pasir dalam tiga hari, sekitar 2165*3/900=7 siklus; ukuran butir setiap siklus berubah sekitar 0.22 (per penggilingan); oleh karena itu, pasir 24 Januari AFS =52.44, ketika ukuran partikel pasir cetak mencapai 52-53, penambahan pasir baru secara terus menerus 70/140 memiliki sedikit pengaruh pada sistem pasir AFS; mulai dari 26 Januari 140/70 pasir baru ditambahkan selama tiga hari berturut-turut untuk menyesuaikan, dan 60kg ditambahkan untuk setiap penggilingan, 1 Pada tanggal 28, AFS pasir adalah 54.
(Catatan: Standar perusahaan FAW menetapkan bahwa tingkat pengayakan 70/140 pasir kuarsa 70,100,140 80%, di mana 70,100 pengayakan ≥60%; 140/70 pasir kuarsa 70,100,140 tingkat pengayakan 80%, di mana 100,140 tingkat pengayakan ≥60 % Setiap volume penggilingan adalah 3 ton, dan volume pasir sistem diperkirakan 900 ton)
4. Perbandingan kadar lumpur dan penghilangan debu selama tiga bulan berturut-turut:
Karena iklim dingin di utara dari Februari hingga Maret, debu di pipa pembuangan debu dingin akan mengembun dan mengeras setelah debu panas dihilangkan. Jika pipa tidak dibersihkan tepat waktu, penyumbatan akan sering terjadi, dan debit harian akan bervariasi dari 4 hingga 8 ton. Kandungan lumpur dari sistem pasir sangat berfluktuasi. Selama periode ini, satu-satunya cara untuk meningkatkan kapasitas penghilangan debu dan mengurangi kandungan lumpur adalah dengan meningkatkan volume udara dari peralatan penghilang debu dan pengerukan pipa;
Setelah memasuki bulan April, suhu berangsur-angsur meningkat, fenomena kondensasi dan pemadatan debu tidak lagi muncul, jumlah penghilangan debu secara bertahap stabil, mencapai debit rata-rata 7-8 ton per hari, dan rentang fluktuasi kadar lumpur berkurang;
Kandungan lumpur dari sistem pasir cetak juga dapat dikurangi dengan menambahkan pasir baru atau mengurangi penambahan bahan pembantu. Kerugian dari kedua metode ini akan dijelaskan dalam kesimpulan pengujian.
5. Kesimpulan pengujian
1. Sesuaikan jumlah aksesori pasir yang efektif
Kristal bentonit rusak sampai batas tertentu dengan pemanasan, dan kekuatan ikatan basah jelas akan berkurang setelah menambahkan air dan pencampuran. Setelah dipanaskan pada suhu yang lebih tinggi dan waktu yang lebih lama, struktur kristal bentonit benar-benar hancur, dan menjadi "tanah liat mati" tanpa gaya kohesif. Peningkatan ketebalan pengecoran, rasio pasir-besi yang rendah, suhu penuangan yang tinggi dan waktu pendinginan yang lama semuanya meningkatkan kehilangan pembakaran bentonit.
Cara paling langsung untuk menilai apakah bubuk batubara yang efektif dalam pasir cetakan cukup adalah dengan mengamati kehalusan permukaan pengecoran dan apakah ada pasir yang menempel. Sebagian batu bara di pasir lama terbakar karena panasnya logam cair yang dituangkan dan perlu diisi ulang. Di sisi lain, bahan tambahan baru seperti pasir segar, pasir inti campuran dan bentonit juga perlu ditambahkan untuk mencapai tingkat bubuk batu bara yang efektif. Jumlah total batu bara bubuk yang ditambahkan selama pencampuran pasir adalah jumlah dari kehilangan pembakaran dan jumlah tambahan tambahan. (Bubuk batubara yang efektif setara dengan aditif efektif dalam teks)
2. Penyesuaian ukuran pasir:
Ukuran partikel pasir cetak bertekanan tinggi umumnya 50/140, sedangkan ukuran partikel inti pasir resin sebagian besar 50/100 atau lebih kasar. Pencampuran pasir inti yang berlebihan akan mempengaruhi kekasaran seluruh pasir basah yang lama, yang akan meningkatkan permeabilitas pasir dan kasarnya permukaan coran.
Untuk menjaga ukuran partikel pasir cetak menjadi kasar, partikel dari sistem penghilangan debu dapat didaur ulang menjadi pasir lama. Atau tambahkan pasir baru yang halus untuk menyesuaikan; seperti disebutkan dalam pengecoran, bila AFS pasir cetak mencapai sekitar 48, sesuaikan dengan terus menambahkan 70/140 atau 140/70 pasir baru; namun, karena coran dipecah menjadi inti sistem pasir Jumlah pasir sudah besar. Jika ukuran partikel pasir cetak tidak dikasar hingga tingkat yang tak tertahankan, tidak disarankan untuk menambahkan pasir baru dalam jumlah besar secara terus menerus, jika tidak maka akan mempengaruhi indikator kinerja lain dari sistem pasir cetak (kadar lumpur, jumlah efektif dan kekuatan karena jumlah pasir baru yang berlebihan). ) memiliki pengaruh pada;
3. Penyesuaian kandungan lumpur
Peningkatan kadar lumpur akan menyebabkan permeabilitas pasir cetak menurun, dan fenomena "ledakan gas" akan terjadi selama proses penuangan, dan pengecoran akan terkikis karena ledakan dan pasir lengket. Kandungan lumpur dari sistem pasir cetak tidak boleh terlalu tinggi; kandungan lumpur dari sistem pasir dapat dikurangi dengan mengurangi jumlah bahan pembantu, tetapi pengurangan kandungan bentonit yang efektif akan menyebabkan kekuatan pasir cetak berkurang, dan kemampuan untuk mengangkat dan menahan pasir akan berkurang; Dosis Penurunan yang efektif akan menyebabkan kemampuan anti lengket pasir dari pasir cetak menurun.
Jika Anda menambah jumlah pasir baru yang ditambahkan untuk menyesuaikan kadar lumpur, pertama-tama hitung berapa banyak lumpur yang dihasilkan berbagai bahan yang baru ditambahkan dalam pasir cor, dan kemudian Anda dapat menghitung berapa banyak pasir mentah yang perlu ditambahkan untuk membuat kadar lumpurnya. pasir cetakan memenuhi Peraturan proses.
Seperti disebutkan dalam artikel tersebut, kandungan lumpur dapat dikurangi sebesar 0.1% untuk setiap 30 kg pasir baru yang ditambahkan di pengecoran; Namun, penambahan pasir baru yang berlebihan tidak hanya akan menyebabkan pemborosan biaya, tetapi juga mengurangi proporsi pasir bekas dalam sistem pasir cetak, yang akan mengurangi kinerja pasir cetak. , Pasir cetakan divergen, yang mempengaruhi kemampuan pasir cetakan untuk dicetak, dan fenomena pencucian pasir terjadi selama proses pengecoran;
Oleh karena itu, penulis percaya bahwa itu adalah pilihan terbaik jika kandungan lumpur dari sistem pasir dapat dikontrol dengan menyesuaikan peralatan penghilang debu.
Secara keseluruhan, sistem pasir yang distabilkan harus mampu menghasilkan coran berkualitas tinggi. Melalui konsep ini, kita harus terus menyesuaikan proses pasir cetak sesuai dengan perubahan kondisi produksi untuk memenuhi kebutuhan produksi.
Harap simpan sumber dan alamat artikel ini untuk dicetak ulang: Bagaimana memastikan stabilitas sistem pasir hijau?
Minghe Perusahaan Die Casting didedikasikan untuk memproduksi dan menyediakan Suku Cadang Pengecoran berkualitas dan berkinerja tinggi (kisaran suku cadang die casting logam terutama meliputi: Pengecoran Die Dinding Tipis,Die Casting Kamar Panas,Die Casting Ruang Dingin), Layanan Bulat (Layanan Die Casting,Mesin Cnc,Pembuatan cetakan, Perawatan Permukaan). Setiap pengecoran aluminium kustom, magnesium atau Zamak / seng die casting dan persyaratan coran lainnya dipersilakan untuk menghubungi kami.
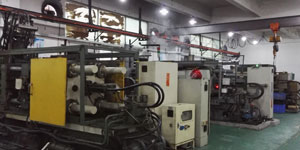
Di bawah kendali ISO9001 dan TS 16949, Semua proses dilakukan melalui ratusan mesin die casting canggih, mesin 5-sumbu, dan fasilitas lainnya, mulai dari blaster hingga mesin cuci Ultra Sonic.Minghe tidak hanya memiliki peralatan canggih tetapi juga profesional tim insinyur berpengalaman, operator dan inspektur untuk membuat desain pelanggan menjadi kenyataan.
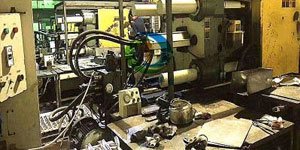
Produsen kontrak die casting. Kemampuannya termasuk bagian die casting aluminium ruang dingin mulai dari 0.15 lbs. hingga 6 lbs., pengaturan perubahan cepat, dan pemesinan. Layanan bernilai tambah termasuk pemolesan, penggetaran, penghalusan, peledakan tembakan, pengecatan, pelapisan, pelapisan, perakitan, dan perkakas. Bahan yang dikerjakan termasuk paduan seperti 360, 380, 383, dan 413.
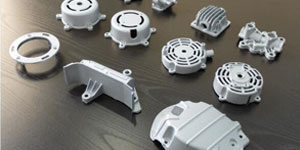
Bantuan desain die casting seng / layanan rekayasa serentak. Produsen kustom pengecoran mati seng presisi. Pengecoran miniatur, coran die tekanan tinggi, coran cetakan multi-slide, coran cetakan konvensional, die unit dan die casting independen dan coran tertutup rongga dapat diproduksi. Pengecoran dapat diproduksi dengan panjang dan lebar hingga 24 inci dalam toleransi +/-0.0005 inci.
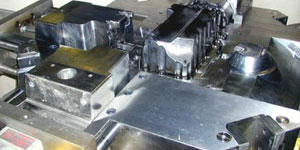
Produsen magnesium die cast bersertifikat ISO 9001: 2015, Kemampuan termasuk die casting magnesium bertekanan tinggi hingga 200 ton ruang panas & 3000 ton ruang dingin, desain perkakas, pemolesan, pencetakan, permesinan, pengecatan bubuk & cair, QA penuh dengan kemampuan CMM , perakitan, pengemasan & pengiriman.
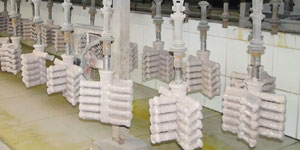
bersertifikat ITAF16949. Layanan Pengecoran Tambahan Termasuk pemilihan investasi,pengecoran pasir,Pengecoran gravitasi, Pengecoran Busa Hilang,Pengecoran Sentrifugal,Pengecoran Vakum,Pengecoran Cetakan Permanen,. Kemampuan termasuk EDI, bantuan teknik, pemodelan solid dan pemrosesan sekunder.
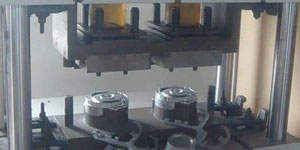
Industri Pengecoran Studi Kasus Suku Cadang untuk: Mobil, Sepeda, Pesawat Terbang, Alat Musik, Perahu, Perangkat Optik, Sensor, Model, Perangkat Elektronik, Penutup, Jam, Mesin, Mesin, Furnitur, Perhiasan, Jig, Telekomunikasi, Pencahayaan, Perangkat Medis, Perangkat Fotografi, Robot, Patung, Peralatan Suara, Peralatan Olahraga, Perkakas, Mainan, dan lainnya.
Apa yang dapat kami bantu untuk Anda lakukan selanjutnya?
Pergi Ke Beranda Untuk Die Casting Cina
→Bagian casting-Cari tahu apa yang telah kita lakukan.
→Tips Terkait Tentang Layanan Die Casting
By Produsen Die Casting Minghe |Kategori: Artikel Bermanfaat |Bahan Tags: Pengecoran Aluminium, Pengecoran Seng, Pengecoran Magnesium, Pengecoran Titanium, Pengecoran Stainless Steel, Pengecoran Kuningan,Pengecoran Perunggu,Video Transmisi,sejarah perusahaan,Aluminium Die Casting |Komentar Dinonaktifkan