Pemesinan Pemotongan Bagian Metalurgi Serbuk (P / M)
Penggunaan proses metalurgi serbuk (P/M) untuk pembuatan suku cadang untuk sistem tenaga otomotif terus berkembang. Bagian yang diproduksi oleh proses P / M memiliki banyak keunggulan penting dan unik. Struktur berpori sisa yang sengaja ditinggalkan di bagian ini bagus untuk pelumasan sendiri dan insulasi suara. Paduan kompleks yang sulit atau tidak mungkin dibuat dengan proses pengecoran tradisional dapat diproduksi dengan menggunakan teknologi P/M. Suku cadang yang diproduksi oleh teknologi ini biasanya memiliki sedikit atau tanpa kapasitas pemrosesan, yang membuatnya lebih murah dan lebih sedikit limbah dalam bahan. Sayangnya, di balik daya tarik fitur tersebut, suku cadang P/M sulit dikerjakan mesin.
Meskipun salah satu tujuan awal industri P/M adalah untuk menghilangkan semua pemrosesan, tujuan ini belum tercapai. Sebagian besar bagian hanya dapat "mendekati bentuk akhir" dan masih membutuhkan beberapa finishing.
Namun, dibandingkan dengan coran dan tempa, sejumlah kecil bahan yang perlu dikeluarkan dari bagian P / M adalah bahan tahan aus yang khas.
Struktur berpori adalah salah satu karakteristik yang membuat bagian p/M memiliki berbagai kegunaan, tetapi umur pahat juga akan rusak oleh struktur berpori. Struktur berpori dapat menyimpan minyak dan suara, tetapi juga menyebabkan pemotongan intermiten mikro. Saat bergerak maju mundur dari lubang ke partikel padat, ujung pahat terus-menerus terkena benturan, yang dapat menyebabkan deformasi fraktur kelelahan yang sangat kecil dan tepi halus runtuh di sepanjang tepi potong. Lebih buruk lagi, partikelnya biasanya sangat keras. Bahkan jika kekerasan makro dari bahan yang diukur adalah antara 20 dan 35 derajat, ukuran partikel dari komponen tersebut setinggi 60 derajat. Partikel keras ini menyebabkan keausan tepi yang parah dan cepat. Banyak bagian p / M dapat diolah dengan panas, dan kekerasan dan kekuatan material lebih tinggi setelah perlakuan panas. Akhirnya, karena teknologi sintering dan perlakuan panas serta gas yang digunakan, permukaan material akan mengandung oksida dan/atau karbida yang keras dan tahan aus.
Kinerja bagian P / M
Sebagian besar sifat bagian P / M, termasuk kemampuan mesin, tidak hanya terkait dengan komposisi kimia paduan, tetapi juga dengan tingkat porositas struktur berpori. Porositas banyak bagian struktural hingga 15% 20%. Porositas bagian yang digunakan sebagai perangkat filtrasi mungkin setinggi 50%. Di ujung seri yang lain, porositas bagian yang ditempa atau pinggul hanya 1% atau kurang. Bahan-bahan ini menjadi sangat penting dalam aplikasi otomotif dan pesawat karena mereka dapat mencapai tingkat kekuatan yang lebih tinggi.
Kekuatan tarik, ketangguhan dan keuletan paduan P / M akan meningkat dengan meningkatnya kepadatan, dan kemampuan mesin juga dapat ditingkatkan, karena porositas berbahaya bagi ujung pahat.
Peningkatan tingkat porositas dapat meningkatkan kinerja insulasi suara bagian. Osilasi redaman di bagian standar berkurang secara signifikan di bagian P / M, yang sangat penting untuk peralatan mesin, pipa tiup AC, dan alat pneumatik. Porositas tinggi juga diperlukan untuk roda gigi yang melumasi sendiri.
Kesulitan dalam pemesinan
Meskipun salah satu tujuan dari pengembangan industri P / M yang berkelanjutan adalah untuk menghilangkan pemesinan, dan salah satu daya tarik utama dari proses P / M adalah hanya sedikit pemrosesan yang diperlukan, banyak bagian yang masih memerlukan pasca perawatan untuk mendapatkan akurasi yang lebih tinggi atau permukaan akhir yang lebih baik. Sayangnya, pengerjaan bagian-bagian ini sangat sulit. Sebagian besar masalah yang dihadapi disebabkan oleh porositas. Porositas menyebabkan kelelahan mikro pada ujung tombak. Ujung tombak terus-menerus memotong masuk dan keluar. Ini melewati antara partikel dan lubang. Benturan kecil yang berulang menyebabkan retakan kecil pada ujung tombak.
Retakan kelelahan ini tumbuh sampai ujung tombak runtuh. Jenis mikro chipping edge ini biasanya sangat kecil, dan biasanya menunjukkan keausan abrasif yang normal.
Porositas juga mengurangi konduktivitas termal bagian P / M, yang menghasilkan suhu tinggi pada ujung tombak dan menyebabkan keausan kawah dan deformasi. Struktur berpori yang terhubung secara internal menyediakan jalur untuk pembuangan cairan pemotongan dari area pemotongan. Hal ini dapat menyebabkan retakan panas atau deformasi, terutama pada pengeboran.
Peningkatan luas permukaan yang disebabkan oleh struktur berpori internal juga menyebabkan oksidasi dan / atau karbonisasi selama perlakuan panas. Seperti disebutkan sebelumnya, oksida dan karbida ini keras dan tahan aus.
Struktur berpori juga memberikan kegagalan pembacaan kekerasan bagian, yang sangat penting. Ketika kekerasan makro bagian P / M diukur dengan sengaja, itu termasuk faktor kekerasan lubang. Struktur keropos menyebabkan runtuhnya struktur dan memberikan kesan yang salah pada bagian yang relatif lunak. Partikelnya jauh lebih keras. Seperti dijelaskan di atas, perbedaannya sangat dramatis.
Adanya inklusi di bagian PM juga merugikan. Selama pemesinan, partikel-partikel ini akan ditarik ke atas dari permukaan, dan goresan atau goresan akan terbentuk di permukaan bagian ketika digosok di depan alat. Inklusi ini biasanya besar, meninggalkan lubang yang terlihat di permukaan bagian.
Perbedaan kandungan karbon menyebabkan inkonsistensi machinability. Misalnya, kandungan karbon paduan fc0208 berkisar antara 0.6% hingga 0.9%. Sejumlah bahan dengan kandungan karbon 0.9% relatif keras, menghasilkan masa pakai alat yang buruk. Batch bahan lainnya dengan kandungan karbon 0.6% memiliki masa pakai alat yang sangat baik. Kedua paduan berada dalam kisaran yang diijinkan.
Masalah pemesinan terakhir berkaitan dengan jenis pemotongan yang terjadi pada bagian P/M. Karena bagian tersebut mendekati bentuk akhir, kedalaman pemotongan biasanya sangat dangkal. Ini membutuhkan ujung tombak yang bebas. Penumpukan chip di ujung tombak sering menyebabkan chipping mikro.
Teknologi pengolahan
Untuk mengatasi masalah ini, beberapa teknologi (khusus untuk industri) diterapkan. Struktur berpori permukaan sering disegel oleh infiltrasi. Pemotongan bebas tambahan biasanya diperlukan. Baru-baru ini, teknik produksi bubuk yang lebih baik yang dirancang untuk meningkatkan kebersihan bubuk dan mengurangi oksida dan karbida selama perlakuan panas telah digunakan.
Struktur berpori permukaan tertutup dicapai dengan logam (biasanya tembaga) atau infiltrasi polimer. Telah berspekulasi bahwa infiltrasi bertindak sebagai pelumas. Sebagian besar data eksperimen menunjukkan bahwa keuntungan sebenarnya terletak pada penutupan struktur berpori permukaan dan dengan demikian mencegah kelelahan mikro dari ujung tombak. Pengurangan obrolan meningkatkan umur pahat dan permukaan akhir. Penggunaan infiltrasi yang paling dramatis menunjukkan peningkatan 200% dalam umur pahat saat struktur berpori ditutup.
Aditif seperti MNS, s, MoS2, MgSiO3 dan BN diketahui dapat meningkatkan umur pahat. Aditif ini meningkatkan kemampuan mesin dengan memudahkan chip untuk terpisah dari benda kerja, memecahkan chip, mencegah penumpukan chip dan melumasi ujung tombak. Meningkatkan jumlah aditif dapat meningkatkan kemampuan mesin, tetapi mengurangi kekuatan dan ketangguhan.
Teknologi atomisasi bubuk untuk mengontrol sintering dan gas tungku perlakuan panas memungkinkan untuk menghasilkan bubuk dan bagian yang bersih, yang meminimalkan terjadinya inklusi dan karbida oksida permukaan.
Bahan alat
Alat yang paling banyak digunakan dalam industri P / M adalah bahan yang tahan aus, tahan retak tepi dan bebas chip di bawah kondisi permukaan akhir yang baik. Karakteristik ini berguna untuk setiap operasi pemesinan, terutama untuk suku cadang P / M. Bahan perkakas yang termasuk dalam kategori ini adalah perkakas cubic boron nitride (CBN), uncoated and coated cermets, dan enhanced coated sintered cemented carbides.
Alat CBN menarik karena kekerasan dan ketahanan ausnya yang tinggi. Alat ini telah digunakan selama bertahun-tahun dalam pengolahan baja dan besi cor dengan kekerasan Rockwell 45 ke atas. Namun, karena sifat unik dari paduan P / M dan perbedaan yang signifikan antara kekerasan mikro dan kekerasan makro, alat CBN dapat digunakan untuk bagian P / M dengan kekerasan Rockwell 25. Parameter kuncinya adalah kekerasan partikel. Ketika kekerasan partikel melebihi Rockwell 50 derajat, alat CBN tersedia terlepas dari nilai kekerasan makro. Keterbatasan yang jelas dari alat ini adalah kurangnya ketangguhan. Dalam hal pemotongan terputus-putus atau porositas tinggi, diperlukan penguatan tepi termasuk chamfering negatif dan pengasahan berat. Pemotongan ringan sederhana dapat dilakukan dengan ujung tombak yang diasah.
Ada beberapa bahan CBN yang efektif. Bahan dengan ketangguhan terbaik terutama terdiri dari seluruh CBN. Mereka memiliki ketangguhan yang sangat baik, sehingga dapat digunakan untuk roughing. Keterbatasan mereka biasanya terkait dengan permukaan akhir. Hal ini sangat ditentukan oleh partikel CBN individu yang membentuk alat. Ketika partikel jatuh dari ujung tombak, mereka akan mempengaruhi permukaan material benda kerja. Namun, tidak begitu serius sehingga alat partikel halus jatuh dari satu partikel.
Material CBN yang biasa digunakan memiliki kandungan CBN yang tinggi dan ukuran partikel yang sedang. Pisau finishing CBN adalah butiran halus, dan konten CBN rendah. Mereka paling efektif ketika pemotongan ringan dan permukaan akhir diperlukan atau ketika paduan yang diproses sangat keras.
Dalam banyak aplikasi pemotongan, umur pahat tidak tergantung pada jenis material. Dengan kata lain, material CBN apa pun dapat mencapai umur pahat yang serupa. Dalam kasus ini, pemilihan material terutama didasarkan pada biaya terendah dari setiap ujung tombak. Satu bilah bundar memiliki seluruh permukaan atas CBN dan dapat menghasilkan empat atau lebih ujung tombak, yang lebih murah daripada empat bilah CBN bertatahkan.
Ketika kekerasan bagian P / M lebih rendah dari Rockwell 35 derajat, dan kekerasan partikel berada dalam kisaran, cermet biasanya menjadi salah satu pilihan. Cermet sangat keras, dapat secara efektif mencegah penumpukan chip dan dapat menahan kecepatan tinggi. Selain itu, karena cermet selalu digunakan untuk pemesinan baja dan baja tahan karat berkecepatan tinggi dan selesai, cermet biasanya memiliki alur geometris yang ideal yang cocok untuk bagian yang dekat dengan bentuk.
Sermet hari ini rumit dalam metalurgi, dengan hingga 11 elemen paduan. Mereka biasanya disinter dari partikel TiCN dan perekat Ni Mo. TiCN memberikan kekerasan, ketahanan pembentukan chip, dan stabilitas kimia yang penting untuk keberhasilan penggunaan sermet. Selain itu, alat-alat ini biasanya memiliki kandungan perekat yang tinggi, yang berarti memiliki ketangguhan yang baik. Singkatnya, mereka memiliki semua karakteristik pemrosesan paduan P / M secara efektif. Beberapa jenis cermet efektif, seperti tungsten carbide sintered cemented carbide, semakin tinggi kandungan pengikat, semakin baik ketangguhannya.
Perkembangan yang relatif baru diketahui adalah bahwa deposisi uap kimia suhu menengah (mtcvd) juga memberikan keuntungan bagi industri P/M. Mtcvd mempertahankan semua ketahanan aus dan ketahanan aus kawah dari deposisi uap kimia tradisional (CVD), tetapi juga meningkatkan ketangguhan secara objektif. Peningkatan ketangguhan terutama berasal dari penurunan retak. Lapisan diendapkan pada suhu tinggi dan kemudian didinginkan dalam tungku. Lapisan mengandung retakan saat pahat mencapai suhu kamar karena ekspansi termal yang tidak konsisten. Mirip dengan goresan pada kaca datar, retakan ini mengurangi kekuatan ujung tombak. Suhu deposisi mtcvd yang lebih rendah menyebabkan frekuensi retak yang lebih rendah dan ketangguhan yang lebih baik dari ujung tombak.
Ketika substrat pelapis CVD dan pelapis mtcvd memiliki karakteristik dan pembalut tepi yang sama, perbedaan ketangguhannya dapat ditunjukkan. Ketika digunakan dalam aplikasi di mana ketangguhan tepi diperlukan, kinerja pelapisan mtcvd lebih baik daripada pelapisan CVD. Melalui analisis, saat mengerjakan bagian P / M dengan struktur berpori, ketangguhan tepi menjadi penting. Lapisan mtcvd lebih baik daripada lapisan CVD.
Lapisan deposisi uap fisik (PVD) lebih tipis dan kurang tahan aus dibandingkan lapisan mtcvd atau CVD. Namun, lapisan PVD dapat menahan dampak signifikan dalam aplikasi. Pelapisan PVD efektif ketika pemotongan adalah keausan abrasif, CBN dan sermet terlalu rapuh dan membutuhkan penyelesaian permukaan yang sangat baik.
Misalnya, ujung tombak karbida semen C-2 dapat dikerjakan dengan mesin fc0205 pada kecepatan garis 180 m / mnt dan laju umpan 0.15 mm / putaran. Setelah pemesinan 20 bagian, penumpukan chip dapat menyebabkan keruntuhan mikro. Ketika lapisan PVD titanium nitrida (TIN) digunakan, penumpukan chip tertahan dan umur pahat diperpanjang. Ketika pelapis timah digunakan untuk pengujian ini, karakteristik keausan abrasif dari bagian P / M diharapkan lebih efektif dengan pelapisan TiCN. TiCN memiliki ketahanan pembentukan chip yang hampir sama dengan timah, tetapi lebih keras dan lebih tahan aus daripada timah.
Struktur berpori penting dan mempengaruhi kemampuan mesin dari paduan fc0208. Ketika struktur dan karakteristik berpori berubah, bahan pahat yang berbeda memberikan keuntungan yang sesuai. Ketika densitasnya rendah (6.4g/cm3), kekerasan makronya rendah. Dalam hal ini, karbida disemen berlapis mtcvd memberikan umur pahat terbaik. Kelelahan mikro ujung tombak sangat penting, dan ketangguhan ujungnya sangat penting. Dalam hal ini, pisau cermet ketangguhan yang baik memberikan umur pahat yang maksimal.
Saat memproduksi paduan yang sama dengan kepadatan 6.8g/cm3, keausan abrasif menjadi lebih penting daripada retak tepi. Dalam hal ini, pelapisan mtcvd memberikan umur pahat terbaik. Karbida disemen berlapis PVD digunakan untuk menguji dua jenis bagian yang sangat keras, dan akan pecah saat menyentuh ujung tombak.
Ketika kecepatan meningkat (kecepatan linier lebih dari 300 meter per menit), cermet dan bahkan cermet yang dilapisi akan menghasilkan keausan kawah. Karbida disemen berlapis lebih cocok, terutama ketika ketangguhan ujung tombak dari karbida disemen berlapis baik. Pelapisan Mtcvd sangat efektif untuk semen karbida dengan area kaya kobalt.
Cermet paling sering digunakan dalam belokan dan membosankan. Karbida disemen berlapis PVD ideal untuk pemesinan ulir karena kecepatan yang lebih rendah dan lebih banyak perhatian pada penumpukan mungkin diharapkan.
Harap simpan sumber dan alamat artikel ini untuk dicetak ulang:Pemesinan Pemotongan Bagian Metalurgi Serbuk (P / M)
Perusahaan Pengecoran Minghe berdedikasi untuk memproduksi dan menyediakan Suku Cadang Pengecoran berkualitas dan berkinerja tinggi (kisaran suku cadang die casting logam terutama meliputi: Pengecoran Die Dinding Tipis,Die Casting Kamar Panas,Die Casting Ruang Dingin), Layanan Bulat (Layanan Die Casting,Mesin Cnc,Pembuatan cetakan, Perawatan Permukaan). Setiap pengecoran aluminium kustom, magnesium atau Zamak / seng die casting dan persyaratan coran lainnya dipersilakan untuk menghubungi kami.
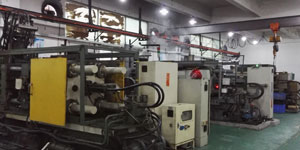
Di bawah kendali ISO9001 dan TS 16949, Semua proses dilakukan melalui ratusan mesin die casting canggih, mesin 5-sumbu, dan fasilitas lainnya, mulai dari blaster hingga mesin cuci Ultra Sonic.Minghe tidak hanya memiliki peralatan canggih tetapi juga profesional tim insinyur berpengalaman, operator dan inspektur untuk membuat desain pelanggan menjadi kenyataan.
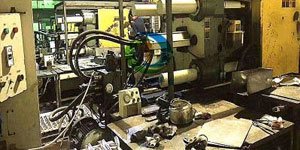
Produsen kontrak die casting. Kemampuannya termasuk bagian die casting aluminium ruang dingin mulai dari 0.15 lbs. hingga 6 lbs., pengaturan perubahan cepat, dan pemesinan. Layanan bernilai tambah termasuk pemolesan, penggetaran, penghalusan, peledakan tembakan, pengecatan, pelapisan, pelapisan, perakitan, dan perkakas. Bahan yang dikerjakan termasuk paduan seperti 360, 380, 383, dan 413.
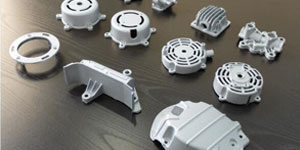
Bantuan desain die casting seng / layanan rekayasa serentak. Produsen kustom pengecoran mati seng presisi. Pengecoran miniatur, coran die tekanan tinggi, coran cetakan multi-slide, coran cetakan konvensional, die unit dan die casting independen dan coran tertutup rongga dapat diproduksi. Pengecoran dapat diproduksi dengan panjang dan lebar hingga 24 inci dalam toleransi +/-0.0005 inci.
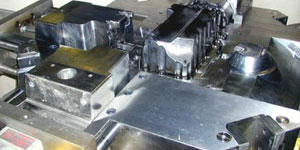
Produsen magnesium die cast bersertifikat ISO 9001: 2015, Kemampuan termasuk die casting magnesium bertekanan tinggi hingga 200 ton ruang panas & 3000 ton ruang dingin, desain perkakas, pemolesan, pencetakan, permesinan, pengecatan bubuk & cair, QA penuh dengan kemampuan CMM , perakitan, pengemasan & pengiriman.
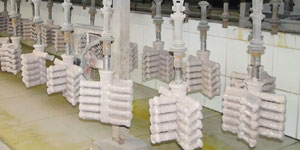
bersertifikat ITAF16949. Layanan Pengecoran Tambahan Termasuk pemilihan investasi,pengecoran pasir,Pengecoran gravitasi, Pengecoran Busa Hilang,Pengecoran Sentrifugal,Pengecoran Vakum,Pengecoran Cetakan Permanen,. Kemampuan termasuk EDI, bantuan teknik, pemodelan solid dan pemrosesan sekunder.
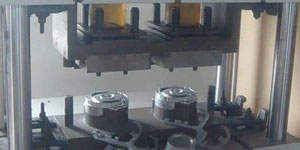
Industri Pengecoran Studi Kasus Suku Cadang untuk: Mobil, Sepeda, Pesawat Terbang, Alat Musik, Perahu, Perangkat Optik, Sensor, Model, Perangkat Elektronik, Penutup, Jam, Mesin, Mesin, Furnitur, Perhiasan, Jig, Telekomunikasi, Pencahayaan, Perangkat Medis, Perangkat Fotografi, Robot, Patung, Peralatan Suara, Peralatan Olahraga, Perkakas, Mainan, dan lainnya.
Apa yang dapat kami bantu untuk Anda lakukan selanjutnya?
Pergi Ke Beranda Untuk Die Casting Cina
→Bagian casting-Cari tahu apa yang telah kita lakukan.
→Tips Terkait Tentang Layanan Die Casting
By Produsen Die Casting Minghe |Kategori: Artikel Bermanfaat |Bahan Tags: Pengecoran Aluminium, Pengecoran Seng, Pengecoran Magnesium, Pengecoran Titanium, Pengecoran Stainless Steel, Pengecoran Kuningan,Pengecoran Perunggu,Video Transmisi,sejarah perusahaan,Aluminium Die Casting |Komentar Dinonaktifkan